Challenges and Best Practices of Warehouse Automation
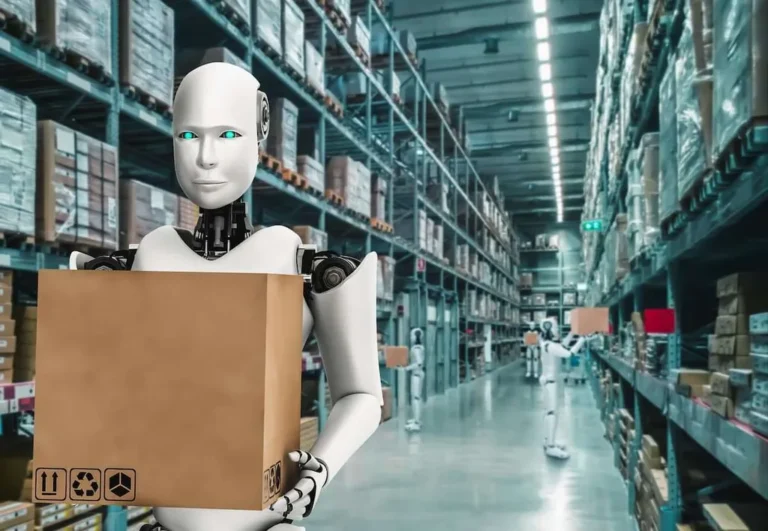
Warehouses are undergoing a technological revolution. It turns them from hubs of manual labor to efficient infrastructures. This wave of automation with artificial intelligence comes in various forms. Today, we see devices that streamline the movement of products from the point of arrival to the point of departure. We also have automated warehouse robots that aid with stock control. If your firm adopts these practices, they may promote timely delivery and reduce labor expenses. Today, we’ll talk about the top practices of warehouse automation and give some tips on how to streamline it.
What is Warehouse Automation, and Why Is It Important
Automation in warehousing entails the methodical substitution of labor-intensive, repetitious tasks for automated technologies. The primary objective is to mitigate resource-draining processes, which affect the overall operational effectiveness. This strategy allows business owners to free up human resources and to concentrate on higher-value tasks.
There are two approaches:
- Digital Automation: It decreases manual labor by optimizing workflows via programs and electronic devices. A warehouse management system (WMS) is one example. It transforms workflow and eliminates the need for human inventory tracking.
- Physical Automation: It streamlines repetitive operations with machines and warehouse robotics. Take, as an illustration, an autonomous mobile robot (AMR). They navigate independently within the storage facilities and fulfill various tasks (transport goods and restock shelves).
In a nutshell, digital transformation improves client service. It streamlines internal operations and enables real-time order status updates. Conversely, physical transformation means no need to engage an extra workforce. People utilize robotic arms for accurate stock control, or robotic storage and retrieval systems for optimal stock management.
Ultimately, AI will clearly play a greater role in logistics automation in the future. Businesses are putting more money into this area; estimates indicate that during the next 5 years, automation solutions will account for a sizable 25% of capital spending.
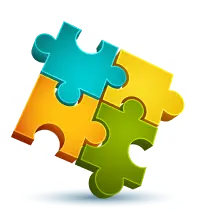
We are confident that we have what it takes to help you get your platform from the idea throughout design and development phases, all the way to successful deployment in a production environment!
How to Automate Your Warehouse
If you’d like to take on automation, you need a well-thought-out strategy. Key stakeholders must actively participate in the strategic plan, which also necessitates a detailed project timetable and well-defined objectives.
The first stage is to assemble a committed support staff and select a project manager. This group will be in charge of creating a timeframe and assigning tasks.
Then, choose the most beneficial warehouse automation systems. The choice hinges upon your firm’s goals, clients’ needs, and the insightful information your team has to provide. The evaluation procedure also requires careful consideration of time limits and available resources. Check out and get demos of different automation alternatives to select the best one.
5 Steps to Automate Your Warehouse
As you take the first steps toward the AI warehouse, you might feel it’s daunting. However, the process can be streamlined and successful with a structured approach. Let’s take a look at a few essential steps to guide you through the initial stages:
Establish a dedicated committee
To ensure effective automation, assemble a committed group with internal stakeholders who have an in-depth understanding of current workflows, available resources, and any technology gaps. Consider adding outside supply chain automation consultants with a strong background in AI in manufacturing, logistics, and industry-specific knowledge to strengthen this team even further.
Collect critical data
A solid foundation of detailed data on the current supply chain and core warehouse activities is essential for data warehouse automation to be effective. Before introducing any new technology, thoroughly assess the present infrastructure and data-gathering procedures.
Check your inventory controls
To level up operations, you need to carefully examine and possibly improve Standard Operating Procedures (SOPs) in critical areas. Well-established SOPs are essential to guaranteeing simplified and practical procedures. Upon optimizing them, one may set up KPIs to evaluate the performance of automated stock management techniques. It’ll show you how automation may affect your existing inventory accounting system.
Install a warehouse management system
A set of software tools called warehouse management systems (WMS) makes stock monitoring and management easier. These technologies monitor warehouse activities and optimize workflows, eventually decreasing labor expenses related to manual labor. To improve accessibility and control, advanced WMS solutions have mobile-friendly and intuitive interfaces.
Figure out what type of automation you want
Is your goal to employ automation to expedite data entry and lower labor expenses in bookkeeping and back-office operations? Are you adding more warehouse space or incorporating additional sites, which has you thinking about robotics and goods-to-person (GTP) systems? For deployment to be seamless, defining the type of warehouse automation that meets the objectives and needs of your clients is critical.
Challenges of Warehouse Automation
Warehouse automation is no easy task. It presents several major hurdles for firms:
- The implementation of automation requires a substantial financial investment. Buying new applications, putting inventory management software into place, and thoroughly educating employees on these cutting-edge technologies, are all major upfront expenses.
- Integration of automation systems with other corporate systems, such as the enterprise resource planning (ERP) system, is necessary. It can be a challenge, as different systems may use different data formats and protocols.
- The industrial regulatory landscape is dynamic. It demands constant adaptation for newly implemented automation systems. Failure to comply with operational standards can lead to non-compliance and a complete halt to operations. It necessitates dedicated resources and continuous monitoring throughout the automation project’s lifecycle. You have to adhere to regulations on data privacy, security, and environmental concerns.
- Staff may ignore the changes and refuse to embrace new warehouse automation technology. Companies must ensure that they have a strategy in place to deal with opposition to transformation within their workforce.
Despite the challenges, organizations may gain a lot from automation. It’s all about greater accuracy, productivity, and functionality. Before you make a final choice, thoroughly analyze the pros and cons of this option and consider all the obstacles.
Warehouse Automation Best Practices
Modern warehouses offer considerable benefits that save expenses and bring client happiness to the next level. To facilitate efficient automation, keep these practices in mind:
- Assure smooth compatibility between your WMS and the automation technologies you have selected. This combination opens the door to a host of simplified operations, including easy labor cost tracking and reporting, centralized supply control, and much more.
- Choose adaptable technology that accommodates your company’s growth. Select a system that can accommodate future growth, such as more employees, equipment, storage space, and changing supply chain agreements.
- Give top priority to technologies that streamline data retrieval, transportation, and storage for a future-proof warehouse. Pocket-sized barcode scanners combined with cloud-hosted programs provide a risk-free route to automation. The ecosystem lays the groundwork for effective expansion — it removes human error and centralizes the workflow of your whole storage facility.
- You should think about redesigning the architecture you already have and incorporate physical automation tech. Automated storage retrieval solutions (AS), GTP, retrieval solutions (RS), and sorting systems can be beneficial. Collaborate with engineers, designers, and solution suppliers proficient in perfecting space and practices.
- Continuous monitoring and optimization of automated systems are essential for maintaining peak performance. Regularly reviewing key performance indicators, identifying bottlenecks, and implementing improvements are critical for ensuring the long-term success of warehouse automation initiatives.
Warehouse administration and supply monitoring tech fuel the automation. It signifies a major turning point in modern logistics. Through the reduction of human involvement in product transportation, these technologies provide flexible supply chains that can efficiently fulfill orders. When you buy these cutting-edge tools and machinery, you let your firm surpass rising client expectations.
Final Words
Modern warehouses are transforming into hubs of efficiency. They’re driven by automation technologies that empower human capabilities. These advancements free up personnel from repetitive tasks and allow them to focus on strategic planning and quality assurance.
GlobalCloudTeam services offer a comprehensive suite of solutions to automate your operations. Our team can guide you through every step. From selecting the right technology to optimizing your existing infrastructure — we’re here to help you. Leverage our proficiency to unlock the full potential of warehouse automation.
Top Articles
RPA as a Service: Features of Robotic Process Automation Outsourcing
I am here to help you!
Explore the possibility to hire a dedicated R&D team that helps your company to scale product development.
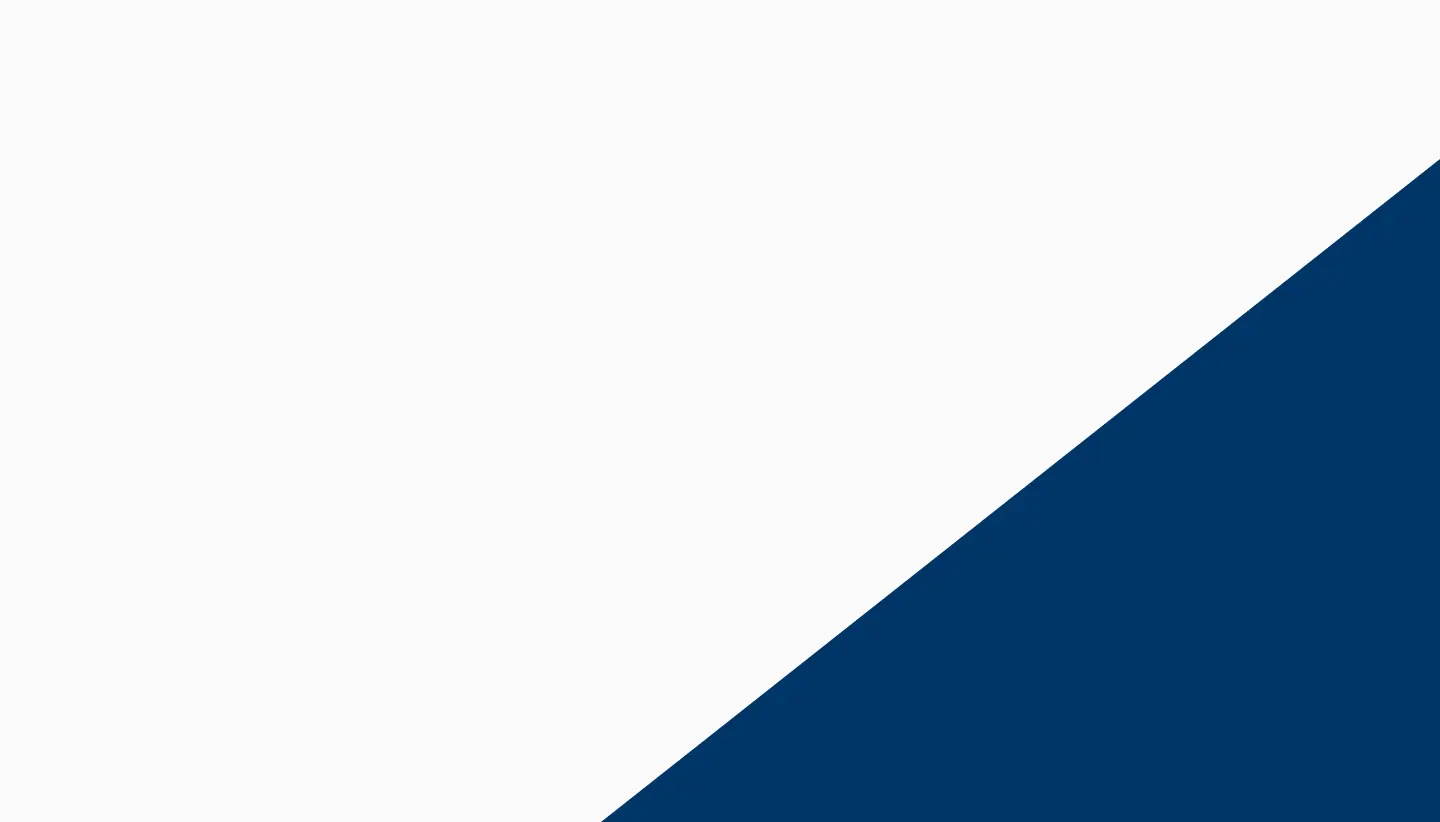
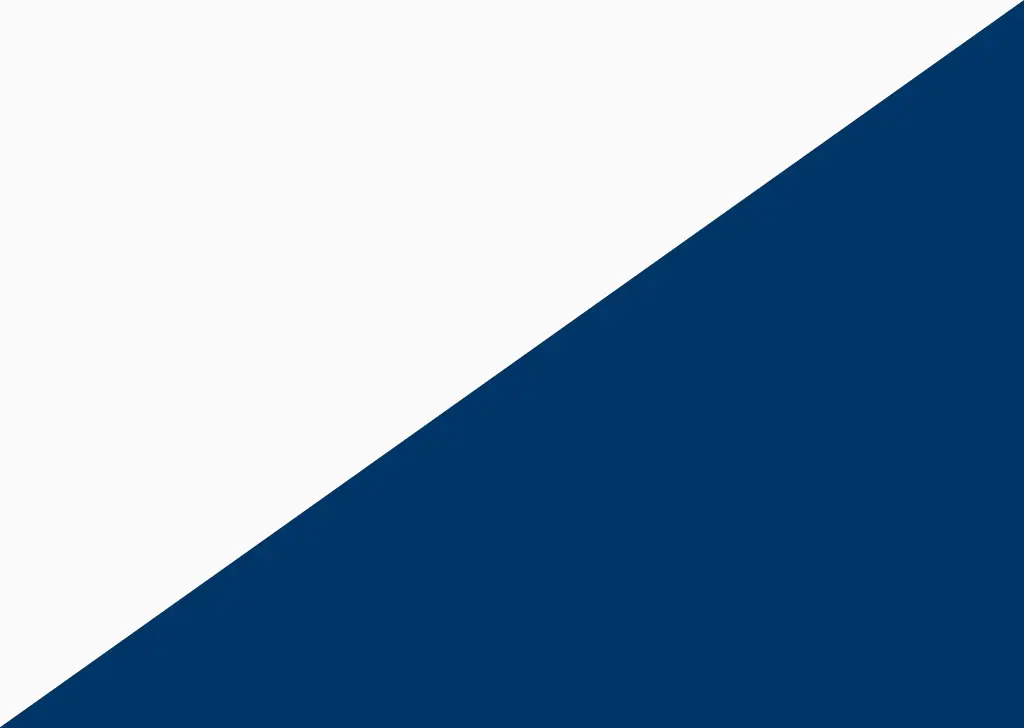